Rony
Moderator
Polycarboxylate (PCE) superplasticizers are known as high range water-reducing admixtures in concretes, such as ready-mix concretes, self-compacting concretes (SCC), ultra-high strength concretes (UHPC) and at the same time give an extended slump retention.
Polycarboxylate Ethers improve the rheology of concrete through the dispersion of particles. Consequently, the water consumption in the mix proportion of concrete is reduced, leading to an improvement of compressive strength and durability of hardened concrete.
This improved concrete technology can be implemented with latest concrete additives.
Admixture is defined as a material other than cement, water and aggregate that is used as an ingredient of concrete and, is added to the batch immediately before or during mixing. It is used to modify properties of concrete according to our required need.
Why Use Concrete Admixtures?
· To increase the strength of concrete
· To accelerate the initial setting time of concrete
· To retard the initial setting time of concrete
· To improve workability of concrete
· To increase durability of concrete
· To reduce heat of hydration
· To make light weight concrete
· To reduce permeability of concrete
· To control the alkali-aggregate expansion
· To increase the resistance to sulphate attack
· To increase the bond between old and new concrete
· To increase the bond between concrete and steel reinforcement
· To reduce segregation and bleeding of concrete
· To produce coloured concrete or mortar
· To control the corrosion of concrete
When Use Concrete Admixtures?
· When properties cannot be made by varying the composition of basic material.
· To produce desired effects more economically.
· Unlikely to make a poor concrete better.
· Not a substitute for good concrete practice.
· Required dose must be carefully determined and administered
How to Use Concrete Admixtures?
· Check job specification
· Use the correct admixture
· Never use one from an unmarked container.
· Keep containers closed to avoid accidental contamination.
· Add the correct dosage.
· Avoid adding ‘a little bit extra
· Use a dispenser
· Wash thoroughly at the end the day
· Best if added to the mixing water
· Manufacturer’s recommended dosage is usually adequate
· Trial mixes are important to determine most effective dosage
Various Types of Chemical Admixtures
History of admixtures is as old as the history of concrete. It embraces a very vast field, bu a few type of admixtures called Water Reducers or High Range Water Reducers.
Water-reducing admixtures are based on a variety of materials; the most common of which are:
As their name implies, the function of water reducing admixture is to reduce the water content of the mix, usually by 5 to 10%, sometimes (in concrete of very high workability) upto 15%. Thus, the purpose of using a water reducing admixture in a concrete mix is to allow a reduction in the water cement ratio while retaining the desired workability or, alternatively, to improve its workability at a given water cement ratio. The actual reduction in water depends on dose of admixtures, cement content, type of aggregate used, ratio of cement, fine and coarse aggregate etc. Therefore, the trial mixes containing an actual material to be used on the job are essential to achieve optimum properties.
The plasticizers are used:
There are four types of super plasticizers that are generally used for concrete as given below:
§ Sulphonated melamine formaldehyde condensates – It is suitable in low temperature areas – dosage: 0.5 – 3% by weight of cement
§ Sulphonated naphthalene formaldehyde condensates – It is more suitable in high temperature areas – dosage: 0.5 – 3% by weight of cement
§ Modified Ligno sulphates – It is suitable for Indian conditions where temperature variation is high – dosage not more than 0.25% by weight of cement
§ Carboxylated admixture – It is suitable where workability is required to be retained for large duration.
HRWR admixtures act in a manner similar to conventional water-reducing admixtures, except that they are more efficient at dispersing fine-grained materials such as cement, fly ash, ground granulated blast-furnace slag, and silica fume. The most widely used HRWR admixtures do not entrain air but may alter the air-void system. Concrete containing HRWR admixtures, however, may have adequate resistance to freezing and thawing even though the spacing factors may be greater than 0.2 mm (0.008 in.). HRWR admixtures based on polyether-polycarboxylate technology are different chemically and more effective than those based on sulfonated melamine-formaldehyde and sulfonated naphthalene-formaldehyde condensates and, as a result, are typically added at the batch plant. Polyether-polycarboxylate HRWRs also retard less and develop strength faster compared to the other HRWR formulations. Because of their increased efficiency, polyether-polycarboxylate HRWRs are gaining widespread acceptance, particularly in precast concrete applications and in making self-consolidating concrete, a high-performance concrete with high flowability that requires minimal or no vibration for consolidation.
A characteristic of some HRWR admixtures is that their slump-increasing effect is retained in concrete for only 30 to 60 min, by which time the concrete will revert to its original slump. The amount of time that the concrete retains the increased slump is dependent upon the type and quantity of cement, the temperature of the concrete, the type of HRWR admixture, the dosage rate used, the initial slump of the concrete, the mixing time, and the thoroughness of mixing. Because of the limited workability time, HRWR admixtures are typically added at the jobsite. With some HRWR admixtures, it is possible to redose the concrete to regain the increased workability. Generally, the strength is increased and the air content is decreased. HRWR admixtures that offer extended slump life are also commercially available. These HRWR admixtures are typically added at the batch plant.
HRWR admixtures can be used with conventional waterreducers or retarders to reduce slump loss and stickiness, especially in silica-fume concrete mixtures. Because a lower dosage of HRWR admixture may be required in such instances, there may be some savings. These combinations of admixtures may also cause unanticipated or excessive set retardation.
The strength of hardened concrete containing HRWR admixtures is normally higher than that predicted by the lower w/cm alone. As with conventional admixtures, this is believed to be due to the dispersing effect of HRWR admixtures on the cement and other cementitious or pozzolanic materials. Because the w/cm of mixtures containing HRWR admixtures are typically low, shrinkage and permeability may also be reduced and the overall durability of the concrete may be increased.
The most recently developed products; the PolyCarboxylate Ethers and Esters additionally work by steric hinderence resulting from the hydrophilic polyether pendent chains which are grafted onto a polyacrylic acid backbone. In total there exists a complex family of PCE products all having influence on rheology, water reduction, workability retention and concrete performance. The user is thus particularly advised to consult the manufacturer before use.
An example of a simple polycarboxylate ester containing polyether side chains;
The modes of action of the new Polycarboxylate Ether (PCE) based superplasticizer effects can be observed below:
In addition, the molecular structures of polycarboxylate superplasticizers can be readily adjusted, so that they can improve the performance of concrete, by providing various desirable features such as adaptability to various temperatures or compatibility with different types of cements, clay resistance, and so forth.
The dispersion effect of traditional water reducing agents, including lignin-based and naphthalene-based water reducers, is primarily due to the repelling effect of double electric layers.
Commonly, polycarboxylate superplasticizers are composed of a backbone chain along with side-chains, which contain both hydrophobic and hydrophilic groups. The hydrophilic groups can be extended into the water phase to form a polymer-based adsorption layer, while the hydrophobic groups can be adsorbed onto the surface of cement particles extend into the air In this context, the interfacial energy between water and a solid or a liquid phase can be substantially reduced, thus promoting dispersion.
It should be noted that steric hindrance is considered to have an important influence on the performance of polycarboxylate superplasticizers.
The polymeric structures of polycarboxylate superplasticizers are usually designed so that they bear long polyoxyethylene ether side-chains to achieve strong steric repulsion, which plays a crucial role in dispersing cement particles. Therefore, the side-chain length of a polycarboxylate superplasticizer has a great influence on its dispersing performance.
Polycarboxylate superplasticizers with longer side-chains can enhance the initial dispersion of cement pastes.
Polycarboxylate superplasticizers with longer side-chains could accelerate the cement hydration process and change the crystal state of the resultant hydration products.
Polycarboxylates Superplasticizers; Polycarboxylates are new generation of concrete admixtures, have more water reducing rate than naphthalene based superplasticizer with better slump retention.
The key to the success of PCE SPs lies in the fact that they offer a broad range of possible molecular structures. Since the molecular structure greatly affects the performance of polycarboxylate ethers, tailoring their molecular structures enables the production of SPs with quite different properties that can be used in a broader range of applications.
The main factors determining the performance of polycarboxylates are:
Polycarboxylate Ethers improve the rheology of concrete through the dispersion of particles. Consequently, the water consumption in the mix proportion of concrete is reduced, leading to an improvement of compressive strength and durability of hardened concrete.
- CONCRETE ADMIXTURES
- POLYCARBOXYLATE COPOLYMERS
Development of Concrete
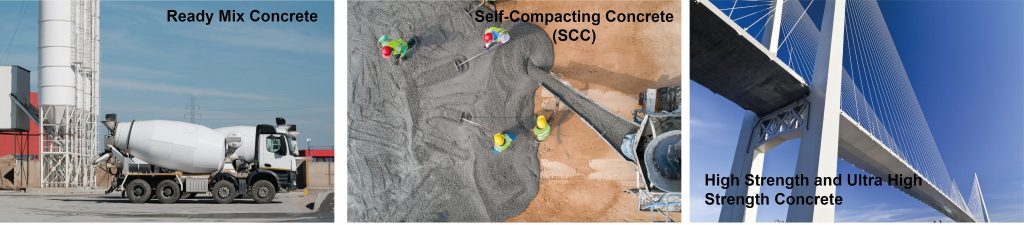
This improved concrete technology can be implemented with latest concrete additives.
Concrete Admixtures
Admixture is defined as a material other than cement, water and aggregate that is used as an ingredient of concrete and, is added to the batch immediately before or during mixing. It is used to modify properties of concrete according to our required need.
Why Use Concrete Admixtures?
· To increase the strength of concrete
· To accelerate the initial setting time of concrete
· To retard the initial setting time of concrete
· To improve workability of concrete
· To increase durability of concrete
· To reduce heat of hydration
· To make light weight concrete
· To reduce permeability of concrete
· To control the alkali-aggregate expansion
· To increase the resistance to sulphate attack
· To increase the bond between old and new concrete
· To increase the bond between concrete and steel reinforcement
· To reduce segregation and bleeding of concrete
· To produce coloured concrete or mortar
· To control the corrosion of concrete
When Use Concrete Admixtures?
· When properties cannot be made by varying the composition of basic material.
· To produce desired effects more economically.
· Unlikely to make a poor concrete better.
· Not a substitute for good concrete practice.
· Required dose must be carefully determined and administered
How to Use Concrete Admixtures?
· Check job specification
· Use the correct admixture
· Never use one from an unmarked container.
· Keep containers closed to avoid accidental contamination.
· Add the correct dosage.
· Avoid adding ‘a little bit extra
· Use a dispenser
· Wash thoroughly at the end the day
· Best if added to the mixing water
· Manufacturer’s recommended dosage is usually adequate
· Trial mixes are important to determine most effective dosage
Types of Concrete Admixtures
Various Types of Chemical Admixtures
- Accelerating admixtures
- Retarding admixtures
- Water-reducing admixtures
- Grouting admixtures
- Air-entraining admixtures
- Super plasticizing admixtures
- Fly ash
- Silica fume
- Ground granulated blast furnace slag
- Rice husk ash
History of Chemical Admixtures
ROMANS | Retarders | Urine |
Air Entrainment | Blood | |
Fibers | Straw | |
PLASTICIZERS | 1930s | Patent for sulphonated naphthalene formaldeyde plasticizers |
PLASTICIZERS | 1930s | Lignosulphanates used as plasticizers |
PLASTICIZERS | 1930s | Hydroxycarboxcilic acid salts used plasticizers and retarders |
WATERPROOFERS | 1930s | Fatty acids, strearates and oleates |
AIR ENTRAINERS | 1941 | Tallow and fatty acid soaps for frost resistance |
SUPERPLASTICIZERS | 1963 | Sulphonated naphthalene formaldehyde patent and available |
SUPERPLASTICIZERS | 1963 | Sulphonated melamice formaldehyde patent and available |
SUPERPLASTICIZERS | 1990-1999 | Polycarboxylate ether development and production |
Water-reducing admixtures are based on a variety of materials; the most common of which are:
- Lignosulfonic acids and their salts;
- Hydroxylated polymers;
- Hydroxylated carboxylic acids and their salts;
- Sulfonated melamine or naphthalene formaldehyde condensates;
Water Reducer Admixtures
A material, which either increases workability of freshly mixed concrete without increasing water cement ratio or maintains workability with a reduced amount of water, is termed as water reducing admixture.As their name implies, the function of water reducing admixture is to reduce the water content of the mix, usually by 5 to 10%, sometimes (in concrete of very high workability) upto 15%. Thus, the purpose of using a water reducing admixture in a concrete mix is to allow a reduction in the water cement ratio while retaining the desired workability or, alternatively, to improve its workability at a given water cement ratio. The actual reduction in water depends on dose of admixtures, cement content, type of aggregate used, ratio of cement, fine and coarse aggregate etc. Therefore, the trial mixes containing an actual material to be used on the job are essential to achieve optimum properties.
The plasticizers are used:
- To achieve a higher strength by decreasing the water cement ratio at the same workability as an admixture free mix.
- To achieve the same workability by decreasing the cement content to reduce the heat of hydration in mass concrete.
- To increase the workability to ease placing in accessible locations.
- Water reduction more than 5% but less than 12%
- The commonly used admixtures are Ligno-sulphonates and hydrocarbolic acid salts.
- Plasticizers are usually based on lignosulphonate, which is a natural polymer, derived from wood processing in the paper industry.
- Plasticizers get adsorbed on the surface of the cement particles and form a thin sheath.
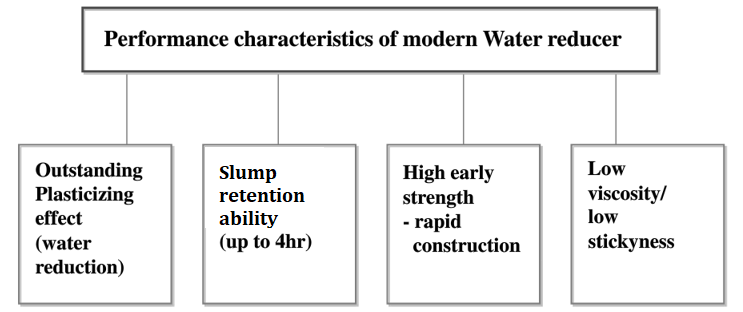
High Performance Water Reducers (HRWR)
Super-plasticizers, also called high range water-reducing admixtures because of their ability to reduce three to four times the mixing water in a given concrete mixture compared to normal water-reducing admixtures, were developed in the 1970s and have found wide acceptance in the concrete construction industry.There are four types of super plasticizers that are generally used for concrete as given below:
§ Sulphonated melamine formaldehyde condensates – It is suitable in low temperature areas – dosage: 0.5 – 3% by weight of cement
§ Sulphonated naphthalene formaldehyde condensates – It is more suitable in high temperature areas – dosage: 0.5 – 3% by weight of cement
§ Modified Ligno sulphates – It is suitable for Indian conditions where temperature variation is high – dosage not more than 0.25% by weight of cement
§ Carboxylated admixture – It is suitable where workability is required to be retained for large duration.
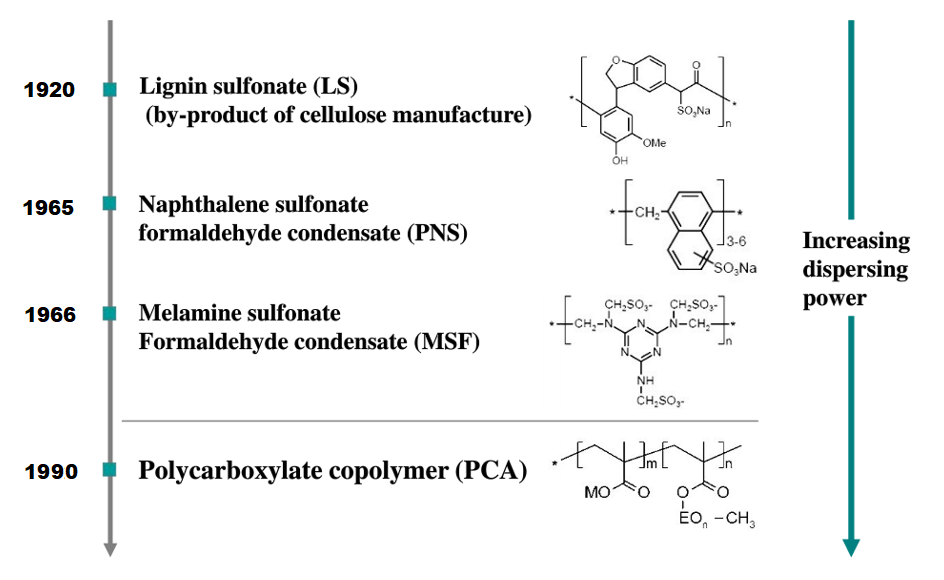
HRWR admixtures act in a manner similar to conventional water-reducing admixtures, except that they are more efficient at dispersing fine-grained materials such as cement, fly ash, ground granulated blast-furnace slag, and silica fume. The most widely used HRWR admixtures do not entrain air but may alter the air-void system. Concrete containing HRWR admixtures, however, may have adequate resistance to freezing and thawing even though the spacing factors may be greater than 0.2 mm (0.008 in.). HRWR admixtures based on polyether-polycarboxylate technology are different chemically and more effective than those based on sulfonated melamine-formaldehyde and sulfonated naphthalene-formaldehyde condensates and, as a result, are typically added at the batch plant. Polyether-polycarboxylate HRWRs also retard less and develop strength faster compared to the other HRWR formulations. Because of their increased efficiency, polyether-polycarboxylate HRWRs are gaining widespread acceptance, particularly in precast concrete applications and in making self-consolidating concrete, a high-performance concrete with high flowability that requires minimal or no vibration for consolidation.
A characteristic of some HRWR admixtures is that their slump-increasing effect is retained in concrete for only 30 to 60 min, by which time the concrete will revert to its original slump. The amount of time that the concrete retains the increased slump is dependent upon the type and quantity of cement, the temperature of the concrete, the type of HRWR admixture, the dosage rate used, the initial slump of the concrete, the mixing time, and the thoroughness of mixing. Because of the limited workability time, HRWR admixtures are typically added at the jobsite. With some HRWR admixtures, it is possible to redose the concrete to regain the increased workability. Generally, the strength is increased and the air content is decreased. HRWR admixtures that offer extended slump life are also commercially available. These HRWR admixtures are typically added at the batch plant.
HRWR admixtures can be used with conventional waterreducers or retarders to reduce slump loss and stickiness, especially in silica-fume concrete mixtures. Because a lower dosage of HRWR admixture may be required in such instances, there may be some savings. These combinations of admixtures may also cause unanticipated or excessive set retardation.
The strength of hardened concrete containing HRWR admixtures is normally higher than that predicted by the lower w/cm alone. As with conventional admixtures, this is believed to be due to the dispersing effect of HRWR admixtures on the cement and other cementitious or pozzolanic materials. Because the w/cm of mixtures containing HRWR admixtures are typically low, shrinkage and permeability may also be reduced and the overall durability of the concrete may be increased.
ADVANTAGES OF HIGH RANGE WATER REDUCERS:
- Significant water reduction;
- Reduced cement contents;
- Increased workability;
- Reduced effort required for placement;
- More effective use of cement;
- More rapid rate of early strength development;
- Increased long-term strength; and
- Reduced permeability.
ADVANTAGES OF HIGH RANGE WATER REDUCERS:
- Significant water reduction;
- Reduced cement contents;
- Increased workability;
- Reduced effort required for placement;
- More effective use of cement;
- More rapid rate of early strength development;
- Increased long-term strength; and
- Reduced permeability.
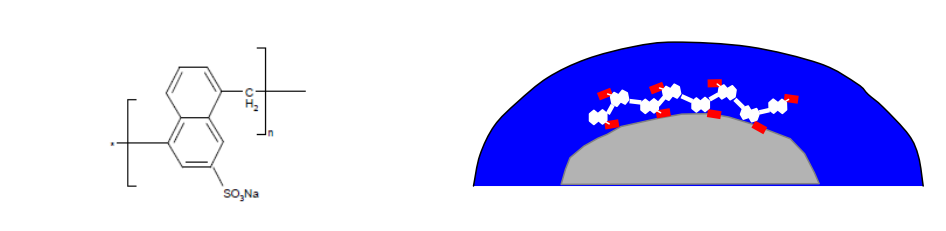
Superplasticizers: The Third Generation – Polycarboxylate Copolymers
Polycarboxylates are complex co-polymers which can be engineered to fulfill many different functions, and consist of a negatively charged ‘backbone’ molecule with polymeric side chains.The most recently developed products; the PolyCarboxylate Ethers and Esters additionally work by steric hinderence resulting from the hydrophilic polyether pendent chains which are grafted onto a polyacrylic acid backbone. In total there exists a complex family of PCE products all having influence on rheology, water reduction, workability retention and concrete performance. The user is thus particularly advised to consult the manufacturer before use.
An example of a simple polycarboxylate ester containing polyether side chains;
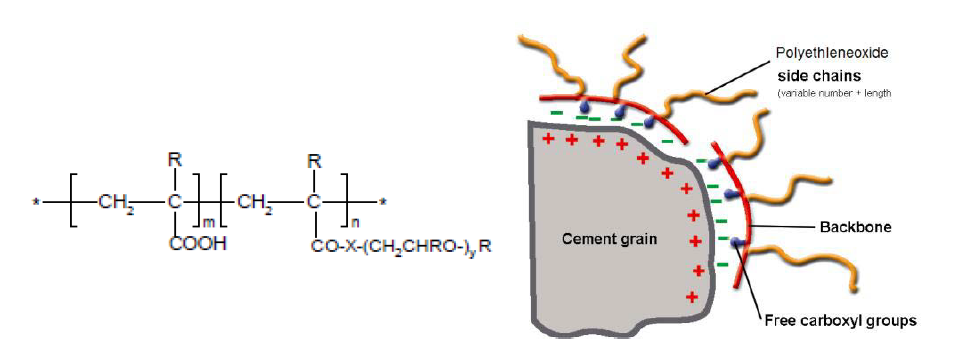
The modes of action of the new Polycarboxylate Ether (PCE) based superplasticizer effects can be observed below:
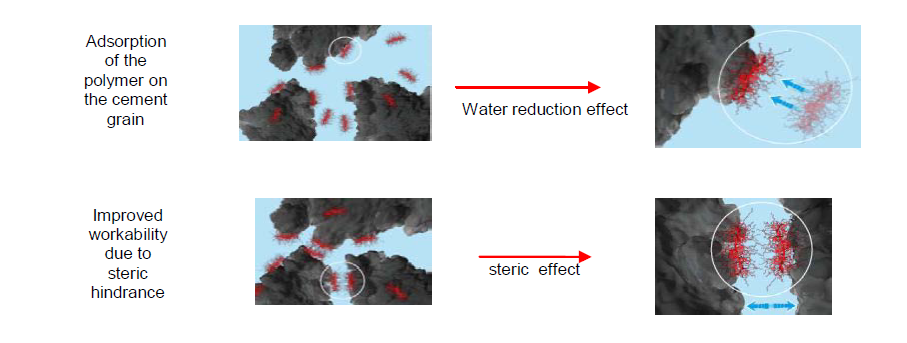
Chemical structure of polycarboxylate superplasticizer and its reaction with cement:
The development of polycarboxylate superplasticizers has advanced rapidly in recent years due to their superior performance and pollutionfree production. The common characteristics of polycarboxylate superplasticizers are their effectiveness at low dosages, high water reducing rates, good plasticity and better concrete shrinkage properties.In addition, the molecular structures of polycarboxylate superplasticizers can be readily adjusted, so that they can improve the performance of concrete, by providing various desirable features such as adaptability to various temperatures or compatibility with different types of cements, clay resistance, and so forth.
The dispersion effect of traditional water reducing agents, including lignin-based and naphthalene-based water reducers, is primarily due to the repelling effect of double electric layers.
Commonly, polycarboxylate superplasticizers are composed of a backbone chain along with side-chains, which contain both hydrophobic and hydrophilic groups. The hydrophilic groups can be extended into the water phase to form a polymer-based adsorption layer, while the hydrophobic groups can be adsorbed onto the surface of cement particles extend into the air In this context, the interfacial energy between water and a solid or a liquid phase can be substantially reduced, thus promoting dispersion.
It should be noted that steric hindrance is considered to have an important influence on the performance of polycarboxylate superplasticizers.
The polymeric structures of polycarboxylate superplasticizers are usually designed so that they bear long polyoxyethylene ether side-chains to achieve strong steric repulsion, which plays a crucial role in dispersing cement particles. Therefore, the side-chain length of a polycarboxylate superplasticizer has a great influence on its dispersing performance.
Polycarboxylate superplasticizers with longer side-chains can enhance the initial dispersion of cement pastes.
Polycarboxylate superplasticizers with longer side-chains could accelerate the cement hydration process and change the crystal state of the resultant hydration products.
Polycarboxylates Superplasticizers; Polycarboxylates are new generation of concrete admixtures, have more water reducing rate than naphthalene based superplasticizer with better slump retention.
Advantages of Polycarboxylic Ethers:
- Low Dosages
- High slump retention
- Water reduction up to 25%
- Good compatibility with cements
- Environmental friendly products
Performance of Polycarboxylic Ethers
The key to the success of PCE SPs lies in the fact that they offer a broad range of possible molecular structures. Since the molecular structure greatly affects the performance of polycarboxylate ethers, tailoring their molecular structures enables the production of SPs with quite different properties that can be used in a broader range of applications.
The main factors determining the performance of polycarboxylates are:
- Length of the backbone
- Chemical nature of the backbone (acrylic, methacrylic, maleic, etc.)
- Length of the side chains
- Chemical nature of the side chains (PEG, polypropylene oxide, etc.)
- Distribution of the side chains along the backbone (random, gradient)
- Anionic charge density
- Linkage between backbone functionalities and side chain (ester, ether, amide, etc.).